Back pressure check valves play a crucial role in various industrial and domestic applications, ensuring that fluid flow is controlled effectively. The significance of these valves can't be overstated, as they are pivotal in maintaining system efficiency and safety. When considering back pressure check valves, it’s essential to focus on key factors such as design, material, and application to ensure optimal performance.
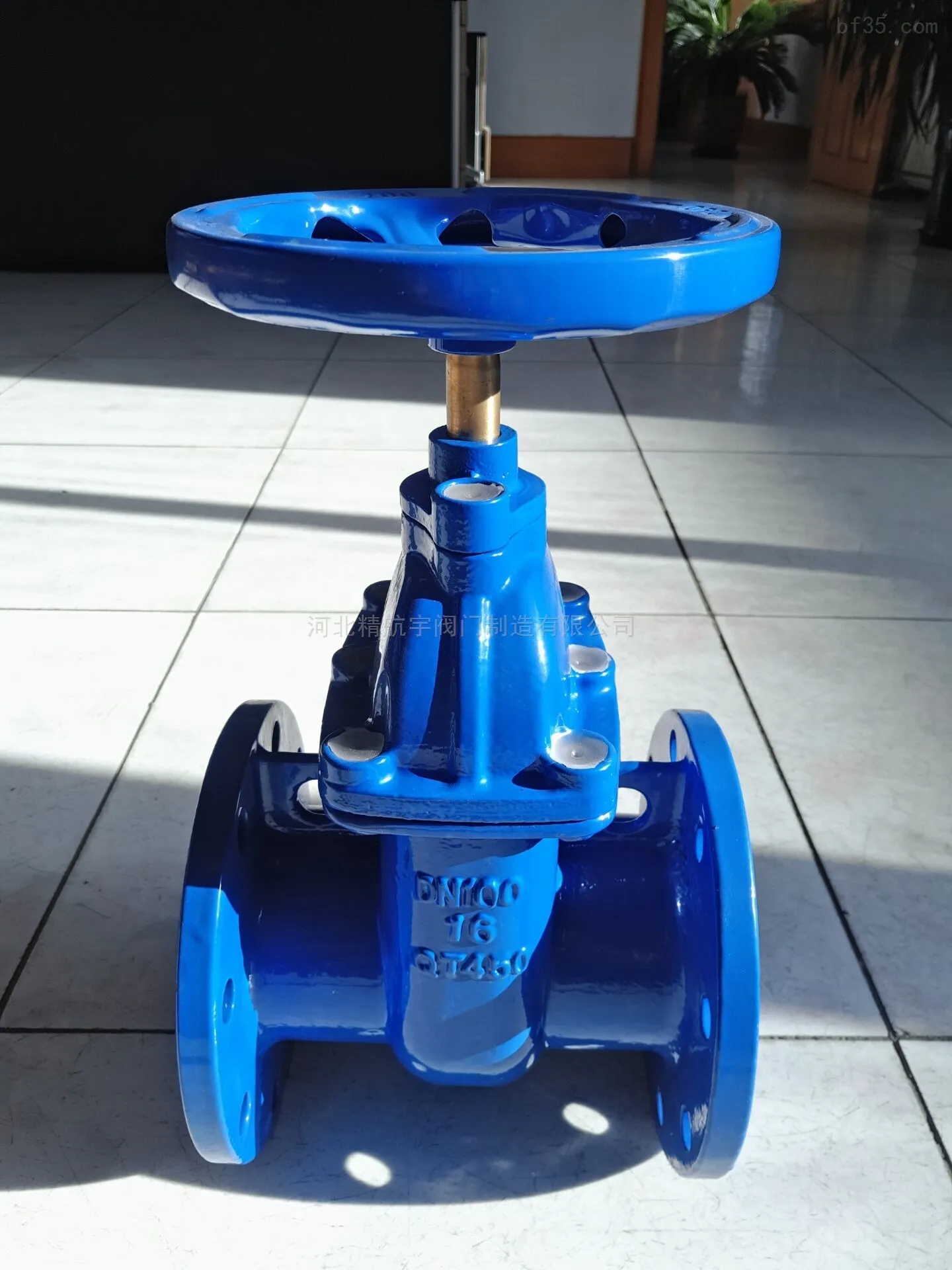
One of the standout features of back pressure check valves is their ability to prevent backflow, thereby protecting the system from potential damage. This is particularly important in systems that handle hazardous or high-pressure fluids. By understanding the specific requirements of your system, you can select a valve that will provide the best performance, enhancing both safety and efficiency.
Back pressure check valves are commonly used in water treatment plants, chemical processing, and oil and gas industries. Their design is crucial to their functionality. Many valves employ a spring-loaded mechanism that ensures responsive and reliable closure, preventing reverse flow under varied pressure conditions. This design minimizes the risk of water hammer, a phenomenon that can lead to costly repairs and downtime.
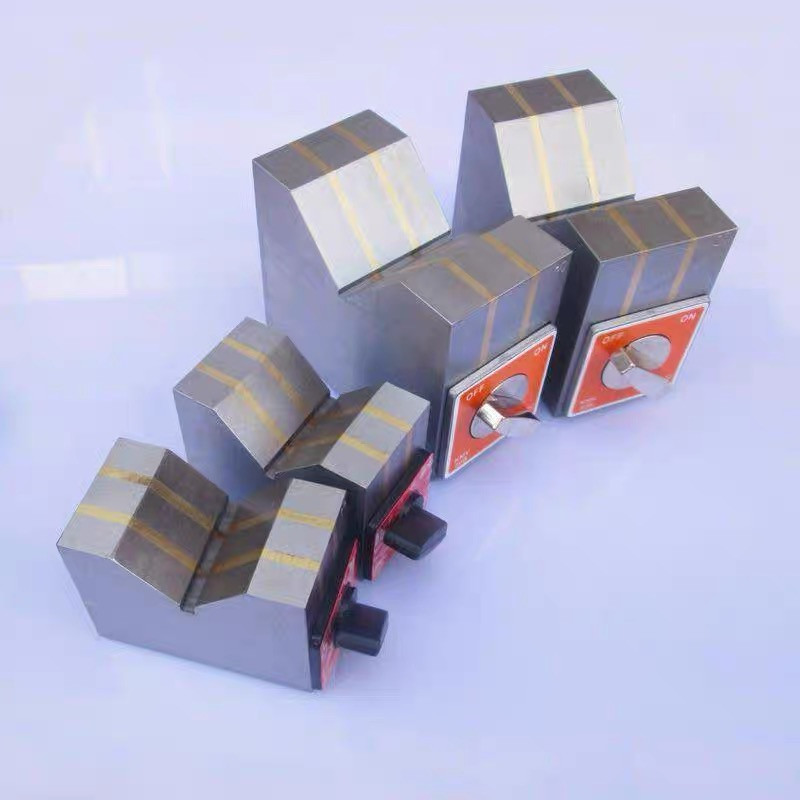
In terms of material selection, compatibility with the fluid being transported is paramount. Stainless steel is often preferred due to its corrosion resistance and durability, making it an ideal choice for harsh and corrosive environments. For systems transporting less aggressive fluids, PVC or other polymer-based materials may be suitable and cost-effective. An expert understanding of material properties and environmental conditions will guide the selection process, ensuring longevity and reliability of the valve.
back pressure check valve
Installation and maintenance are critical components of the lifecycle of back pressure check valves. Proper installation requires precision to avoid leaks and ensure valve efficacy. Engage experienced professionals for installation, as this reduces the likelihood of future operational issues. Regular maintenance, including inspections and cleaning, extends the valve’s lifespan and guarantees consistent performance. Operators should be trained in basic maintenance techniques, which contributes to the overall reliability of the system.
The impact of pressure on valve performance is another consideration. Understanding the pressure range within which a valve will operate is essential for selecting a product that will withstand and regulate such conditions. Many manufacturers provide detailed pressure ratings and performance data to aid in the decision-making process. Leveraging this information helps in choosing a valve that not only meets current needs but can adapt to potential changes in operational demands.
For businesses focused on sustainability, selecting the right back pressure check valve also involves evaluating energy efficiency. Valves designed to operate with minimal energy loss contribute to reduced operational costs and lower environmental impact. Advanced technologies, including smart monitoring systems, are now embedded in valves, providing real-time data that can optimize system performance and preemptively detect issues before they escalate.
Ultimately, the choice of a back pressure check valve should be grounded in the expertise and experience of professionals who understand both the technical requirements and the operational environment. Building a relationship with a reputable supplier who offers comprehensive support and after-sales service ensures that your investment is protected over the long term. By prioritizing efficiency, reliability, and safety, businesses and operators can maintain high performance and protect their systems against the risks associated with backflow and pressure instability.