In the realm of precision measurement tools, micrometres, often known as micrometers or mics, are indispensable. These devices, essential in fields like engineering, manufacturing, and scientific research, facilitate accurate measurements of objects, thereby ensuring quality and precision in various industries. Understanding the different types of micrometres and their specific applications can enhance the selection process and optimize their use for best results.
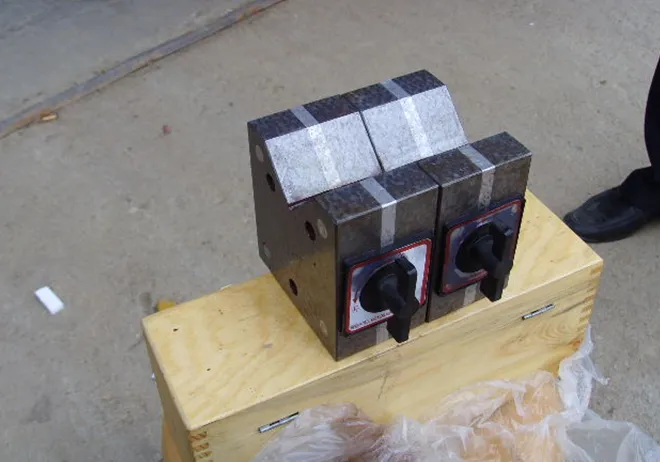
Micrometres come in a variety of forms, each designed to address specific measurement needs. Among the most commonly used types are the outside micrometre, inside micrometre, and depth micrometre, each catering to distinct scenarios. The outside micrometre, perhaps the most recognizable, is designed for measuring the external dimensions of an object, such as the diameter of a cylindrical part. It typically consists of a C-shaped frame, a spindle, and an anvil. The user tightens the spindle until it lightly touches the object, with the resulting measurement displayed on a calibrated scale or digital screen.
Inside micrometres, on the other hand, are engineered to measure the internal dimensions of an object, like the diameter of a bore or the width of a slot. They often include a set of interchangeable rods that extend the measuring range or a set of adjustable anvils that can be set to different widths. This type of micrometre is more complex to use, requiring skill and experience to ensure precise measurements.
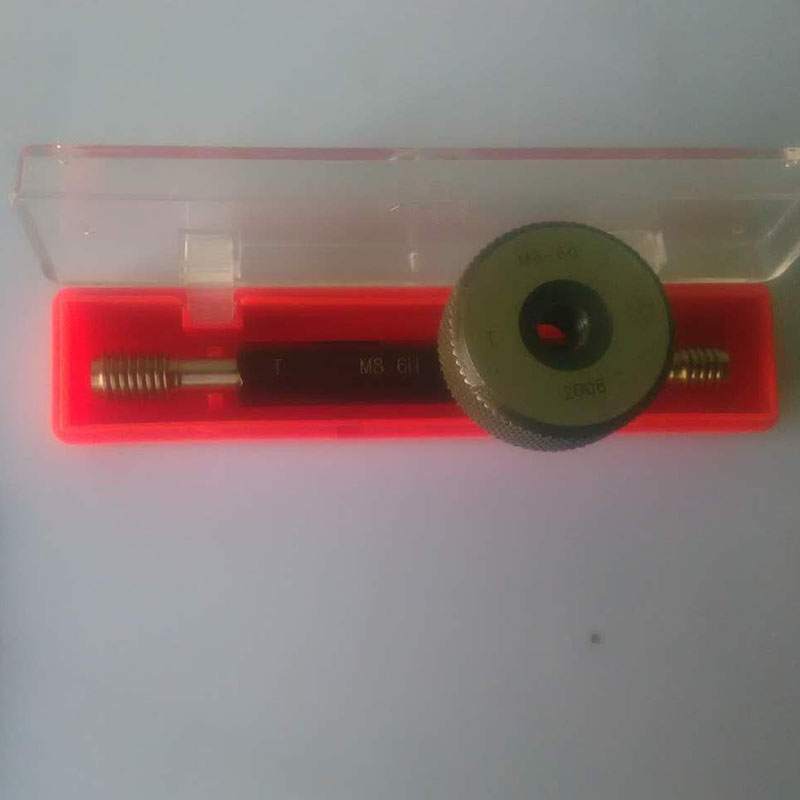
Depth micrometres are particularly essential for gauging the depth of slots or steps. The design includes a flat base that rests on the surface, with a spindle that extends down to measure the depth reliably. Their precision ensures that even the minutest depths can be recorded with consistency, a crucial aspect in fields where precision is paramount.
Each type of micrometre employs a calibrated measuring scale, either mechanical or digital, to allow for precision readings. While traditional mechanical micrometres rely on a graduated barrel, more modern digital micrometres offer an electronic readout, increasing ease of use and minimizing reading errors. The choice between digital and mechanical models often depends on user preference or specific industry requirements.
In the realm of materials, micrometres typically feature hardened steel or stainless steel for durability, with carbide-tipped contact surfaces to resist wear and tear over time. Ensuring longevity and maintaining accuracy are primary concerns, especially in environments where tools are subject to continuous use.
type of micrometre
Accuracy is the cornerstone of micrometre functionality, with most top-tier models offering a precision of up to 0.001 mm or 0.0001 inch. Calibration is a critical process that should not be overlooked; regular verification against a certified gauge block is recommended to ensure ongoing precision. This is particularly important in compliance-driven industries where measurement accuracy is legislated.
The use of micrometres is rooted in the skills and knowledge of the operator. Training in their correct application, understanding potential sources of error, such as temperature variation influencing material expansion, can significantly affect measurement integrity. Proper handling, consistent measurement pressure, and avoiding exposure to extreme temperatures or humidity are essential for maintaining the tool's accuracy.
For organizations seeking to procure micrometres, considering factors such as measurement range, resolution, accuracy, and ease of calibration can guide effective decision-making. It's also worthwhile to explore custom solutions that some manufacturers offer, tailoring tools to meet specific project needs or challenging measuring scenarios.
As technology advances, micrometres continue to improve, with innovations such as wireless connectivity emerging, allowing measurement data to be transmitted directly to computers or data loggers. These advancements not only streamline the data collection process but also enhance real-time decision-making, providing superior value to industries where precision drives quality.
In conclusion, understanding the different types of micrometres, their specific applications, and the precision they offer can empower users to make informed choices and maintain high standards of quality in their respective fields. Selecting the right tool, maintaining its calibration, and ensuring it's operated by knowledgeable personnel can deliver unparalleled accuracy, thus reinforcing the reliability and competitive edge required in today's precision-driven world.